The Withum Way, which defines WithumSmith+Brown PC’s corporate culture and is comprised of a series of “strength” messages,” is prominently displayed throughout the CPA firm’s new Whippany office space via custom graphics and technology. — Courtesy: WithumSmith+Brown PC
By Joshua Burd
WithumSmith+Brown PC has completed the relocation of more than 125 employees to a newly built-out 33,000-square-foot office space in Hanover, the accounting firm said.
In a news release Monday, Withum announced the completion of the move to 200 Jefferson Park in the town’s Whippany section. The firm also touted the sustainable design of the space, which incorporates nearly 43 percent of recycled content and diverts 26,150 pounds of construction waste from landfills.
Kirk Holderbaum, partner-in-charge of the Whippany office, called it “an exciting time for our office and the firm.”
RELATED: Office owner touts tenant activity, campus upgrades
“As was the case with the other recent relocations in our firm, this new office space will accommodate our continued growth and help facilitate the future expansion of our service lines and practice areas,” Holderbaum said. “This ultimately enhances our ability to serve our clients at the highest levels.”
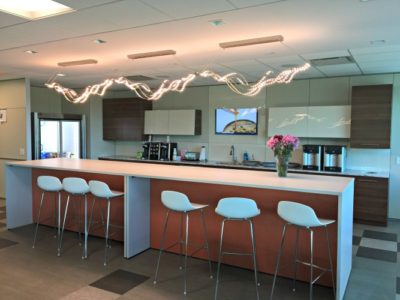
Employees in the new Whippany office have relocated from Morristown. The firm said the project resulted from collaboration with Aztec Total Architecture of Iselin, Interior Construction Partnership of Morristown, a division of Office Furniture Partnership, landlord Vision Real Estate Partners of Mountain Lakes and DIRTT Environmental Solutions.
The team created a modern design that pays tribute to the achievements of past employee generations, the news release said. High-design, high-function elements include integrated television technology, wood walls, dual paint colors and systems related to power, data and plumbing.
“Most importantly, the firm wanted to communicate The Withum Way, which defines its corporate culture and is comprised of a series of ‘strength’ messages,” said Bob Rigby of OFP/DIRTT. “The result: these messages — passion, innovation, community and strength — are prominently displayed throughout the space on custom graphics and via technology that has been integrated into the DIRTT wall systems.”
The news release said DIRTT, a technology-driven manufacturer of customized interiors, is facilitating a construction industry shift toward efficiency by placing as much value on the environment and people as on visual and functional design. The firm uses prefabricated interiors with cost certainty, minimal waste, faster lead times and a precise fit and finish.
In total, 556 pounds of carpet scrap and 25,594 pounds of drywall waste were diverted from landfills, Withum said. The build-out of 2,000 linear feet was completed in five days, with power and data premanufactured and inspection ready, while carpet installation spanned three days in a wide open, warm shell.
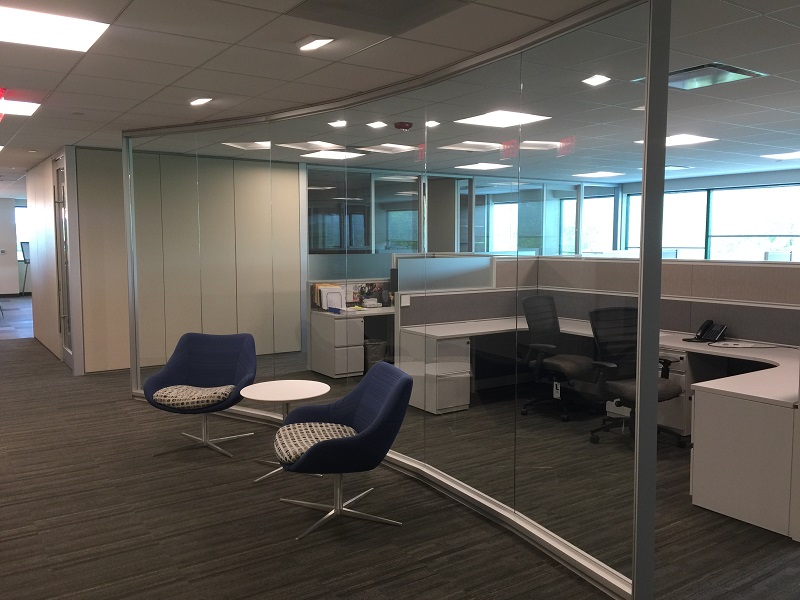